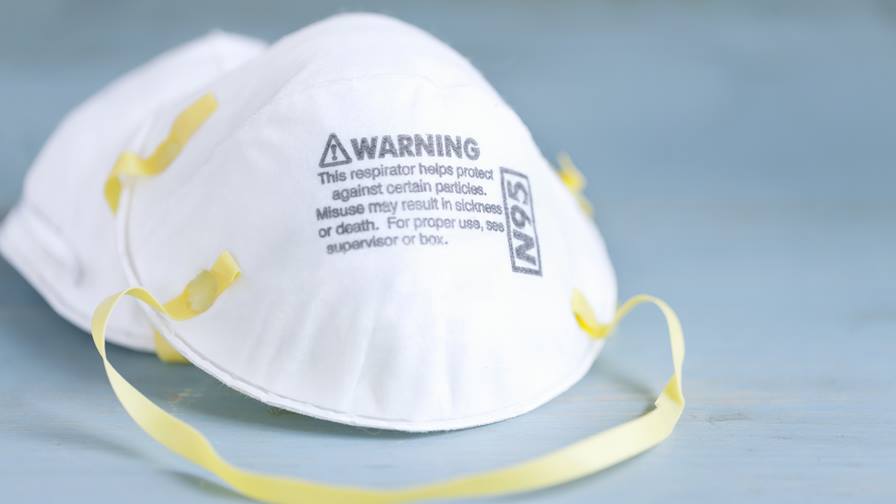
The Safety Management team and Supply Chain Organization, with the help of 145 departments across the organization, have successfully reprocessed and disinfected more than 20,000 N95 respirators to date—helping our caregivers have the PPE they need to safely perform their jobs.
The process to disinfect the respirators takes about 24 hours and can be performed up to five times on a specific N95 respirator. The team has been reprocessing masks seven days a week since April 1, but they’re now moving to five days a week because of the stabilization in COVID-19 cases.
“For many caregivers, the disinfection process has become part of their routine when using an N95 respirator,” says Kellie Furman, project manager. “Once the respirator is disinfected and returned to the facility, the internal logistics need to work well, so the caregivers receive their correct respirator in a timely manner. The caregivers who champion these in-house workflows not only assure that this ‘routine’ runs smoothly for their hospitals and departments, but they also address disruptions that may occur along the way. We’re so thankful for these champions because we couldn’t make this process work across the system without them.
Intermountain was one of the first healthcare institutions to respond to the N95 respirator shortage by mobilizing the Bioquell vaporized hydrogen peroxide decontamination and disinfection process. Because of this effort, caregivers are ensured reliable access to N95 respirators.