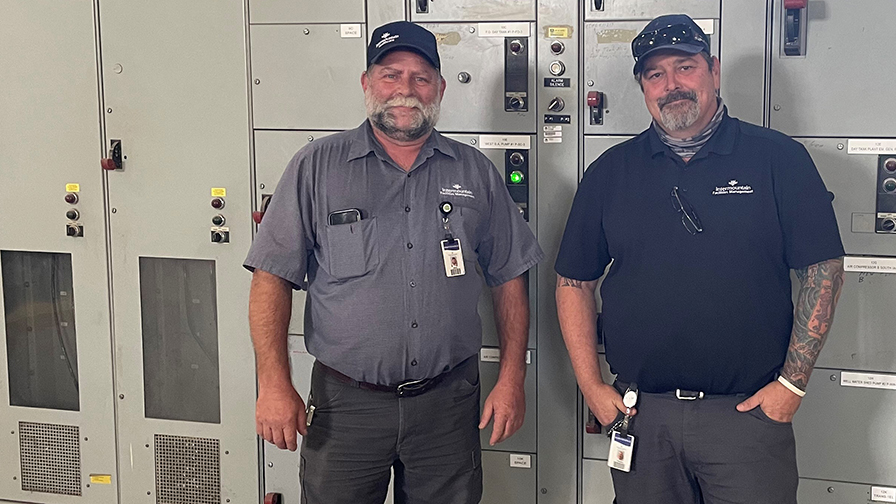
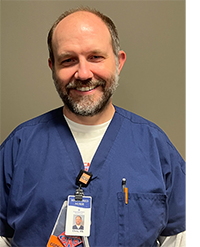
Chris Rosqvist, RN, was the house supervisor that night and he updated caregivers as the lights continued to flicker.
On a recent summer night a device so small that it could be held with one hand afflicted LDS Hospital with power issues for nine hours.
Some patients probably didn’t even notice the lights quietly flickering, but those who were working in protective suits to fix the problem said each time the 12,000-volt transformers were tripped by the malfunctioning device it sounded as if a lightening bolt had struck inside the hospital.
Charles Minnis, equipment system specialist, was one of several people working to fix the problem. He says even when the malfunctioning part tripped things, patients were safe because the hospital was prepared and the facility has back-up power which ensures vital medical equipment remains operational when the power goes out.
Chris Rosqvist, RN, was just beginning his Sunday night shift as house supervisor when the power went off for a few seconds. He thought, at first, it might be related to the electrical storms they’d been having. One of the first calls he made was to Heather Wall, the hospital administrator, but she couldn’t be immediately reached because she was out on a boat at Rockport Reservoir in the middle of a micro storm that cut off her reception.
A text from Chris made it through and Heather sent a follow-up text to Cameron Gabriel, administrative director at LDS Hospital, who immediately went into the hospital to connect with all departments, see what was needed and help wherever he could. Heather went straight to the hospital as soon as she got ashore, connecting with the team that was doing continuous rounds throughout the hospital to assure our patients and our caregivers were safe.
Charles and Mark Peek, maintenance engineer, knew something was amiss before they got any phone calls because the problems triggered several alarms on their phones that immediately sent them over to the hospital. Mark, who had to leave a family birthday party, arrived first. Eventually hospital administrators came in and went around checking on caregivers and patients. They were there for three or four hours early in the morning, Chris says.
“I stayed in contact with my charge nurses and with security and security also stayed in contact with Charles,” Chris says. “I wanted everyone to feel safe and informed and I was just trying to keep everybody in the loop, reminding them we had backup power.”
Heather says Chris played a critical role in keeping people informed.
“From the operating room to the ED, to the ICU, he connected with individuals in each unit and worked with them to help solve problems,” she says.
“Chris had the hard job because he had to communicate and relay all the information,” Charles says. “We’ve got the easy part. We find the equipment that’s broken and we fix it.”
There was nothing easy about fixing this particular problem. They eventually figured out a device called a “tiebreaker’ was giving the transformers bad instructions.
“When the tiebreaker would trip, it sounded like a lightning bolt,” Charles says. “I used to work at IMC and everything there is electronic and computerized, and you can log onto a computer and say, ‘Okay, here is the problem.’ With LDS Hospital, it’s a different sort of animal. You have to physically find the problem and that can get pretty interesting.”
Three vendors were called in and Charles described it as a “collaborative effort” as the experts tried to troubleshoot the problem.
“When you’re working with 12,000 volts you don’t get close to it,” Charles says. “It’s not safe. They had to put on special suits to be able to even touch this stuff. You know when lightening strikes and you get the hairs that stand up on your arm and the back of your neck? That same type of charge was in the room when they were working on it, so it’s a very nerve-wracking feeling.”
When they figured out the tiebreaker was causing the commotion, they soon learned that manufacturers stopped making the part in 1990. It took them until 4 a.m. to come up with a solution, Charles says.
“It was a really small thing,” Charles says of the malfunctioning part. “If you looked at it, you’d be like, ‘No way that should take a whole hospital down.’ But it did a pretty good job of it. In our electrical system we have two 12,000-volt transformers in the back by the loading dock and this piece of equipment is what told those transformers what to do.”
Heather says Charles made sure things were working before he left.
“Charles ensured that chillers, boilers, and air handlers were all back up and running and this translated into patients being able to stay cool in their rooms and it allowed them to wash hands and shower,” Heather says. “His expertise since coming to the team a year ago has been invaluable.”
She says Mark was responding to people with needs and helping them all night.
“Mark did an exceptional job connecting with our nursing teams so they were confident that the environment for our patients would be comfortable and safe, and they would know how to talk with patients about the situation, if that need came up,” she says.
Heather has high praise for the work that Chris, Mark, and Charles did.
“They know our hospital inside and out and because of that our patients were safe and our caregivers felt very supported,” she says. “Their level of expertise is second to none. They didn’t have to stay all-night from when the power started going out until 9 a.m. the next day just to do that. They chose to do that because they wanted to make sure that everything was safe and up and running for our caregivers and our patients.”